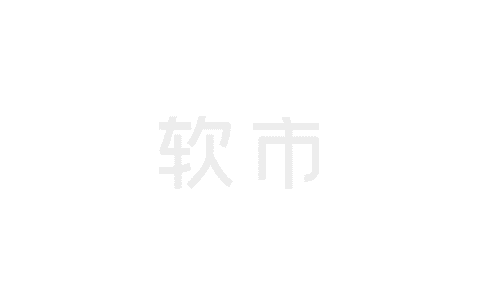
PFMEA的七个步骤为失效模式和后果分析提供了一种系统的分析方法,
第一步,规划和准备,定义分析的范围,选择一个过程作为分析的对象;
第二步:结构分析,将制造系统分解为过程、过程步骤及作业要素;
第三步:功能分析,将功能、产品特性与过程特性适当地分配给各个系统元素;
第四步:失效分析,分析失效模式、失效后果及失效原因,并形成失效链;
第五步:风险分析,确定预防措施与探测措施,并进行SOD的评价,得出AP行动的优先级;
第六步:优化,变更工艺设计,降低严重度及失效原因的发生频度,增加探测失效原因与失效模式的能力,并重新进行SOD评价,获得一个最低的AP行动优先级。
第七步:结果文件化,向客户及管理层汇 分析的结果。
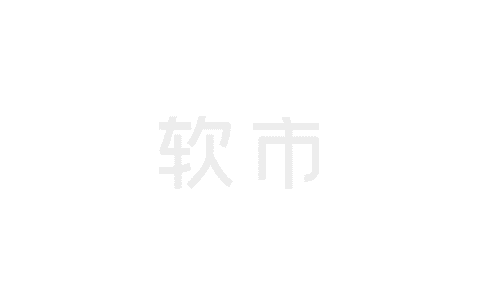
PFMEA第一步,规划与准备阶段,识别项目并定义范围,确定PFMEA包含或不包含哪些过程。
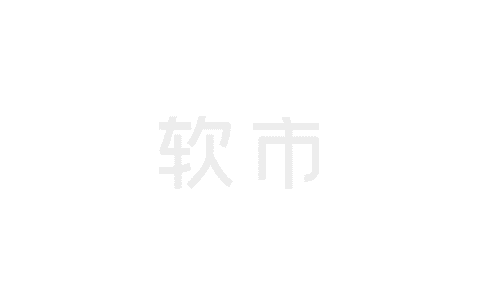
DFMEA第一步:规划与准备步骤的主要目标是:
1、确定项目;
2、项目计划;
3、确定项目的范围,分析中包括哪些过程,不包括哪些过程?
4、根据经验和教训确定基础FMEA;
5、作为结构分析的基础;
以下的提问能帮助我们确定PFMEA的范围:
1、新开发的产品和过程;
2、产品或过程的变更;
3、操作和运行条件的变化;
4、法律法规要求、标准规范、客户等要求的变化;
5、制造经验、工厂内部的质量问题、使用现场问题/保修信息;
6、可能导致危险的过程失效;
7、内部产品监视的结果,如返工、 废;
8、人体工程学的问题;
9、持续改进;
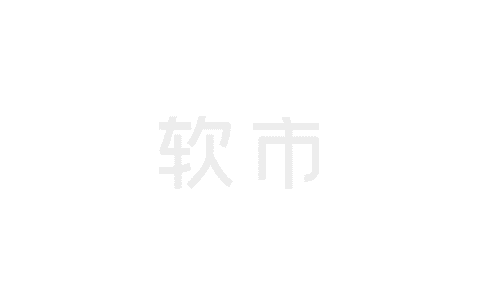
工厂可能影响产品质量的过程,以及考虑用于PFMEA分析的过程包括:
-
接收过程、
-
零件和材料储存、
-
产品和材料交付、
-
制造、
-
装配、
-
包装、
-
标签、
-
成品运输、
-
储存、
-
维护过程、
-
检测过程以及返工
-
返修
-
…
DFMEA项目明确后,应当立即制定PFMEA的执行计划,在制定项目计划时,组织还需考虑适用的顾客的特定要求CSR的进展情况,PFMEA的七步法的过程应纳入项目计划中。
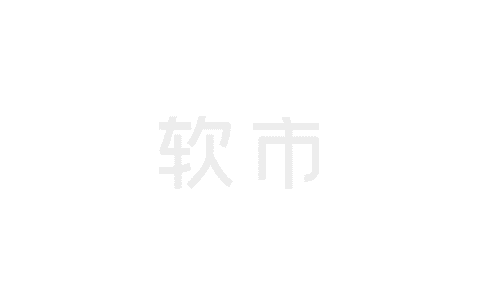
在PFMEA第一步需完成PFMEA的表头,包括了:
-
公司名称、
-
工程地点、
-
顾客名称、
-
车型年/项目、
-
项目、
-
PFMEA开始日期、
-
PFMEA修订日期、
-
跨功能小组、
-
PFMEA ID、
-
过程责任人、
-
保密等级
-
…
其中要重点说明的是PFMEA的开始日期与修订日期,PFMEA的开始与修订应与项目计划保持一致,在充分了解生产概念时,启动PFMEA,在工艺设计决策时,完成PFMEA分析,在PPAP之前,完成PFMEA措施,当现有设计或过程变更时,需重新启动DFMEA和PFMEA计划。
国可RFMEA
R-FMEA是基于业界标准和最佳实践开发而成的失效模式及影响分析软件。它基于FMEA工程应用行业-汽车行业的标准和最佳实践,融合国可工软团队十几年的可靠性咨询和服务经验, 基于产品结构树和工艺流程图,通过向导式的分析过程, 建立产品设计的DFMEA(设计FMEA)和产品制造的PFMEA(工艺FMEA), 并可以扩展到SFMEA(系统FMEA)、MFMEA(机器FMEA)、 FMECA(故障模式、影响和危害性分析)等不同的应用。
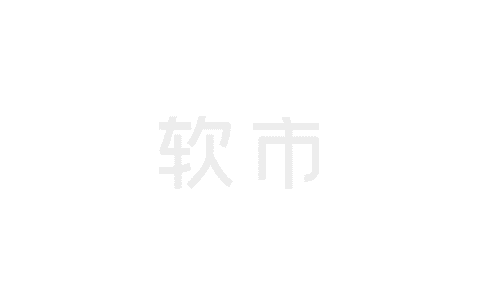
与传统的FMEA分析方法和软件相比,R-FMEA最大的特点是通过其七步的分析流程, 构建了关联紧密的FMEA基础数据关系,即FMEA主模型。FMEA主模型体现了类三维模型概念,既包括了结构之间、功能之间、失效之间的关联关系, 又包括了结构、功能、失效、措施、风险值(S、O、D)之间的关联关系。这些关联关系在分析过程中逐步创建,并保存于底层数据库中。通过FMEA主模型,工程人员可以根据需要构建简单的或者及其复杂的FMEA分析, 并实现企业知识的积累和快速重用。
声明:本站部分文章及图片源自用户投稿,如本站任何资料有侵权请您尽早请联系jinwei@zod.com.cn进行处理,非常感谢!