引言:
伴随着《中国制造2025》的提出与实施,一时间大街小巷似乎人人都在谈论“智能制造”“数字化工厂”,仿佛中国在一夜之间就要进入到工业4.0时代。但是威?赫兹里特曾经说过“伟大的思想只有付诸行动才能成为壮举”。智能工厂的概念很完美,但是只有落到实践处,才能真正展现出价值。而兰光创新则通过携手海尔模具,实现了数字化工厂落地。
企业市场背景简介:
青岛海尔模具有限公司,贵为中国最大的模具及检具制造商,拥有世界领先的产品、模具设计、分析、加工软件以及其他专业的加工设备总计达到250多台。海尔模具在模具制造业享有着无可争辩的王者地位。近些年来海尔模具通过不断地改革升级,大幅度的提高了生产效率,可以实现每个数控操作工同时操作3-4台机床。
客户机遇及挑战:
然而尽管海尔模具身缠效率有了很大的提升,但还是面临着相当大的压力。一方面这样效率的提升源自于车间内部的小修小补,并没有从根本上实现管理或技术上的革新,这样的操作可以在短时间内提升工作效率,但是在忧患意识强烈的海尔人看来,他们需要寻求更好的方式来维持自身的领先地位。另一方面,随着我国模具制造水平的不断提高,市面上逐渐出现更多的模具制造厂商,行业的竞争逐渐变得白热化,产品的逐渐趋同不断地压缩着仅剩的利润空间。
项目需求:
上面的情况迫使海尔模具将目光转移到了企业内部,希望通过“内部挖潜”提升车间管理水平,降低加工过程中对人员技能的要求,特别是建立起车间级的制造过程全面协同管理系统,从而提升企业的盈利空间。
案例信息:
当持有顶尖智能工厂解决方案的兰光创新与渴求管理技术升级的海尔模具最终相遇时,两者碰撞出的将是耀眼的火花。
在听取了兰光创新关于数字工厂建设的介绍后,海尔模具相关负责人直言“这就是他们一直以来苦苦寻找的解决方案”。在做了进一步的了解之后,双方很快便达成了战略合作。
解决方案:
合作达成之后,各种事项便有条不紊的展开。为了更好的了解海尔模具的相关状况,兰光先后几次深入到海尔模具生产车间收集数据,在经历了一段时间的实地考察之后,兰光创新拿出了一套为海尔模具量身制作的解决方案。这套解决方案针对模具行业制造的特点,同时充分的借鉴了德国工业4.0、美国GE工业互联 等先进理念,以设备物联 为核心,以生产管理协同为主线,旨在达成企业生产数字化、智能化、少人化、高效化的目标。这套解决方案中包含着兰光引以为傲的CPS协同制造管理系统,这是兰光创新潜心研究模具制造行业生产管理过程,为模具行业量身打造的包含生产计划、物流、电极、NC程序、刀具准备、加工过程监控等全面事务管理的信息系统。
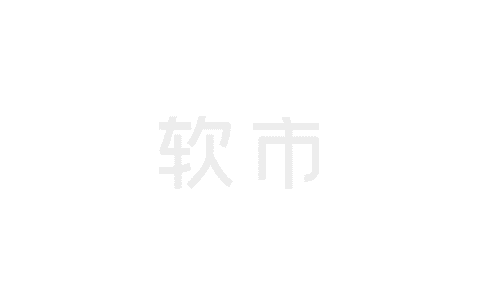
对客户的价值:
海尔负责人认可了兰光解决方案之后,车间很快的便开始实施起一整套的设备物联 系统。经过了一段时间的运营之后,海尔模具将实施效果反馈了回来:
- 优化生产组织模式,加工准备由串行方式优化为并行,管理上变得更加的扁平化,生产效率得到了很大的提升,缩短了至少50%的生产准备时间。
- 实时系统后,操作工1人可以操作5台设备,用工数量减少了25%。
- 实现了100%的程序自动传输,程序调用错误率控制在万分之一以下,设备有效利用率平均达到了75%以上。这已经远远地超出国内企业。
40%的平均水平,也高于欧美发达国家的70%的标准。
这样的效果无疑是可喜的,对于海尔模具而言,减少了的是用工数量、无用时间,提升了的则是生产效率与利润水平;而对于整个制造业行业而言,这无异于一场变革。兰光创新在海尔模具的智能工厂建设的案例则产生了拨云见日的效果,如此成功的智能工厂落地方略对整个行业起到了良好的借鉴作用。
海尔模具总经理对次智能工厂落地方案给予了高度评价:“系统不仅帮助了海尔模具建成了国内领先的智能工厂,企业实现了高效、少人化的管理,取得了很好的经济效益,现在,海尔模具已经成为了海尔集团信息化建设的一面旗帜!”
声明:本站部分文章及图片源自用户投稿,如本站任何资料有侵权请您尽早请联系jinwei@zod.com.cn进行处理,非常感谢!