

利用西门子 QMS 的质量功能有效评估设计和流程中的风险
高层摘要
在汽车行业,设计和制造缺陷可能会产生严重后果,例如增加保修成本、损害产品功能和行车安全、无法达到必要行业标准等。因此,是否能够评估产品和流程中潜在故障所带来的风险,对于企业生存与发展至关重要。故障模式和影响分析 (FMEA) 是一种有效评估和预防风险的重要工具。如果能够在成品下线之前充分考虑并解决所有质量问题,开发人员和制造商就可以避免在生产后期进行设计更改,从而提高生产质量,节约成本。如果能有一款功能强大的 FMEA 闭环质量解决方案,汽车开发人员和制造商就可以进行完整风险分析,降低风险和成本。Siemens Digital Industries Software 推出了一款与协作平台紧密集成的质量管理系统 (QMS), 可以确保从一开始就把事情做对,避免以后出现麻烦情况。
序言
汽车市场变幻莫测,挑战与机遇并存
在产品和流程的质量开发方面,汽车行业正面临不断加快的市场变化和日益增长的行业挑战。在此环境下,汽车制造商如何才能保证汽车产品的质量、问责和兼容性?
这些挑战虽令人生畏,但同时又伴随着有助于提升企业竞争力的机遇。涵盖这些挑战和机遇的市场趋势包括全球市场的不可预测性和日益个性化的量产等。由于激烈的市场竞争(尤其是新兴市场和顶级供应商的外包垄断),单车利润在不断减少。
此外,数字化和颠覆性技术也对汽车制造商造成了一定冲击。因此,他们亟需提高数字化水平,以交付更多创新产品并处理复杂的制造需求,而这些创新又可开启新机遇,提高绩效和质量水平。此外,汽车制造商及其供应商还必须交付零缺陷组件和系统,并按照国际汽车工作组 (IATF) 16949 等汽车标准进行质量管理。
同时,这些外部挑战也让原始设备制造商 (OEM) 和一级供应商 (FTS) 倍感压力,因为他们既要提高产品质量,又要实现快速交付,还要降低成本。
美国国家公路交通安全管理局 (NHTSA)《2020 年度召回 告》1显示,由缺陷和合规性问题导致的召回在过去几年不断增加,涉及车辆、设备、儿童座椅和轮胎等产品。相关数据进一步印证了这一趋势。“仅在 2019 年,就有 881 次召回(涉及 3850 万辆汽车),高于 2010 年 647 次召回(涉及 1970 万辆汽车)。”
实施新创新会有哪些风险?随着未来技术成为汽车厂商常规操作的一部分,FMEA 必须考虑哪些新场景?
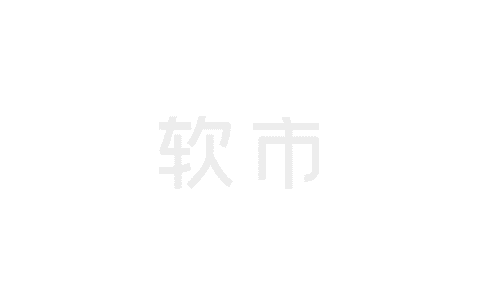
图 1.市场变幻莫测,挑战与机遇并存。
四大关键制造挑战
这些市场趋势对汽车行业质量的综合影响可以归纳为四大关键挑战。这些挑战都可以通过一体化数字质量方法成功解决。
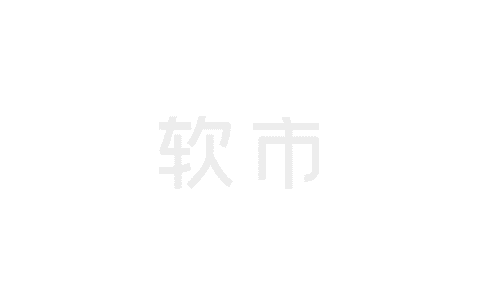
图 2.关键挑战。
-
打破工程、制造和质量部门之间的信息孤岛。
-
实现企业所有活动的可追溯性。
-
建立囊括企业各领域相关数据的通用存储库。
-
建立通用的更改管理流程。
质量管理:从分散式走向一体
与其他复杂制造业相比,汽车行业在自动化和数字化方面一向走在前面。相当一部分汽车企业已经实施了包括质量管理在内的数字化解决方案。然而,其中许多系统是由企业自制而成,未采用一体化方法,也无法纳入标准化的平台。
而由多种过时、分散系统组成的碎片化质量体系势必会让企业的一切努力大打折扣、甚至付之东流。要想改善这一情况,制造商就要充分借鉴和利用标准质量典范做法。此外,他们还需要采用数字化方法进行质量管理,显著降低质量或绩效低下的风险。
对于所有制造商及其供应商而言,拥有贯穿整个产品生命周期的闭环质量解决方案至关重要。这样他们不仅能够应对开发和制造过程中的各种挑战,还可以确保实现其业务目标。
为此,西门子专门打造了一个产品组合,可支持整个产品生命周期的数字化转型和端到端质量管理。西门子 QMS 可利用该产品组合的多个元素,将设计流程与车间制造有机连接到一起。
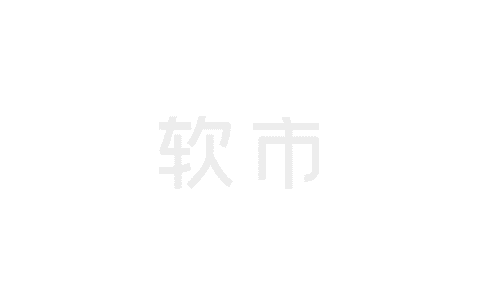
图 3.跨领域一体化质量视图。
持续不断的信息流:端到端
产品和流程的质量对实现企业目标至关重要。质量决定了制造商的竞争力。要想达到高质量标准,企业就要能够在从概念设计到实现再到成熟的整个产品生命周期中持续改进质量流程。
为此,西门子将其传统“策划-实施-检查-改进”(PDCA) 循环从 QMS 扩展到了工程和制造领域。此一体化解决方案可用于开发过程的各个阶段,大幅提升产品和流程的质量和效率。
为支持上述端到端质量管理,西门子 QMS 在生产生命周期的四个阶段都提供强大的质量功能:
阶段 1:保质设计 – 使用现代化开发方法,按照从系统到逻辑结构再到虚拟产品的顺序依次开发产品。产品质量在设计阶段就已确定好。质量要求应在系统工程过程中制定并纳入到 3D 模型中,用于综合公差分析。质量信息以产品制造信息 (PMI) 形式与下游流程相关联。将质量数据集成到设计过程早期可让企业在竞争力和成本效益方面具有更大优势。
阶段 2:质量策划 – 质量团队应采取一切必要措施了解客户需求,并据此设计优质的产品和流程。此策划有助于汽车制造商避免后期项目更改,提高质量并降低成本。在质量策划阶段,西门子 QMS 可用于处理先期产品质量策划 (APQP) 和 FMEA 等关键策划任务。
阶段 3:质量执行 – 要想产品达到预期质量标准,除完美产品策划外,还要善于控制生产和供应流程。
阶段 4:质量改进 – 实际产品的任何偏差都应记
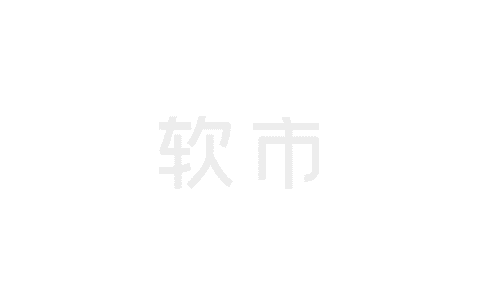
图 4.跨领域一体化质量流程。
通过控制所有流程,制造商可以提高响应速度和产品合格率,并避免多个部门或工厂之间信息重复或丢失。
由此可见,制造商或其供应商可以通过控制流程来提高质量一致性。
闭环 QMS 如何支持 FMEA 准备和实现在质量策划阶段,汽车企业需要考虑其日常业务活动中的多种风险,避免发生召回等负面事件,损害其品牌形象。
这些风险可能来自:
-
引进新设备或对生产流程进行重大更改
-
推出新产品、新材料或新技术
-
出于降低成本目的更换外包组件的备选供应商
根据汽车行业适用质量标准和准则,企业需要对所有关键流程和决策进行风险量化和考量。对于风险管理,国际标准化组织 (ISO) 9001:2015 虽未规定具体方法,但强调了其重要性。IATF 16949:2016 则提出了一种具体方法,将 FMEA 用作主要风险识别工具。鉴于制造商会将 FMEA 应用于各种情况,有必要了解适用标准和准则在风险处理方面的预期要求。这些标准和准则并未硬性规定企业要消除所有风险,而是希望企业能够识别、记录和管理相关风险。
作为企业评估其产品或流程潜在故障相关风险的一种方法,FMEA 主要应用于设计和流程领域,可在产品推出过程中识别、量化及控制风险。
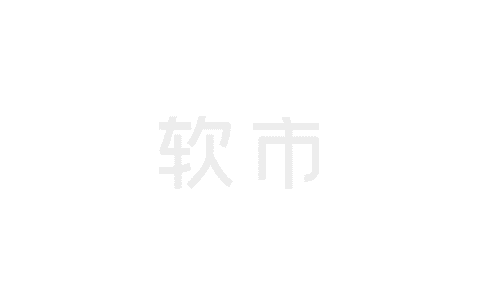
图 5.专注于质量策划阶段。
其中,设计故障模式和影响分析 (DFMEA) 可识别新产品开发过程中的潜在故障,并在早期加以规避或缓解,而流程故障模式和影响分析 (PFMEA) 则可识别制造流程中的风险,并尽可能地降低风险。无论采用哪种分析方法,跨学科质量团队都会对故障进行评估,然后通过以下三步流程反复衡量相关风险和机遇:
5 . 识别潜在故障。
6 . 分析故障几率及相关后果。
7. 采取改进措施消除故障原因,降低故障几率。
作为一种前瞻性的质量方法,首先要了解客户的质量需求,然后才能设计产品和流程。在策划和设计产品时,质量团队必须回答以下问题:
-
产品或流程都有哪些必须考虑的相关特征?
-
产品或流程都有哪些关键质量特征?
-
我们的质量目标是什么?该如何实现这些目标?
-
潜在故障是什么?它们会对成品或最终用户产生什么影响?
-
如何将主要开发问题传达给最高管理层?
-
如何向利益相关者说明我们处理相关风险的优先顺序?
-
各部门是否都配备了管理产品或流程开发所需的专业知识和人员?
要解决这些问题,首先就要组建质量团队,其中包括核心团队和扩展团队,他们将基于 FMEA 进行风险评估。这些团队应跨部门组建,并由协调员(通常称为 FMEA 调解人)领导。团队成员可能包括企业各部门(质量、制造、研发、采购、维护和服务等)专家和关键组件供应商。
相比之下,西门子 QMS 的一体化方法则不存在此问题,可将所有活动从繁琐的纸质操作转化为轻松常见的用户体验。通过响应式的用户界面 (UI),团队成员可在自己的计算机上查看关键信息。此西门子解决方案摒弃了使用分散式工具在企业内部人工追踪多个质量活动的传统做法,转而使用集中式数据库来存储所有质量相关数据。
借助西门子 FMEA,质量人员可使用树形结构和 状图表构建复杂的设计和流程,对各层级的数据进行排序分类,并实现快速高效的复杂结构导航。质量团队可以定义系统元素、功能和故障。用户可以创建链接来验证故障的原因和后果,从而采取相应的预防和检测行动。此外,还可以显示产品、组件、部件及功能与故障之间联系的详细列表。
声明:本站部分文章及图片源自用户投稿,如本站任何资料有侵权请您尽早请联系jinwei@zod.com.cn进行处理,非常感谢!