目的
过程失效分析旨在识别失效起因、模式和影响,并展示它们之间的关系,以便进行风险评估。
过程失效分析的主要目标是:
? 建立失效链
? 每个过程功能的潜在失效影响、失效模式和失效起因
? 使用鱼骨图(4M类型)或失效 识别过程失效起因
? 顾客和供应商之间的协作(失效影响)
? FMEA表格中失效文件化和风险分析步骤的基础
每个过程要素/步骤(结构分析/步骤二和功能分析/步骤三)都会执行失效分析。
失效
过程步骤失效源于产品和过程特性。示例包括:
? 不符合要求
? 不一致或部分被执行的任务
? 没有目标的活动
? 不必要的活动
失效链
针对特定失效,需考虑以下三个方面:
? 失效影响(FE)
? 失效模式(FM)
? 失效起因(FC)
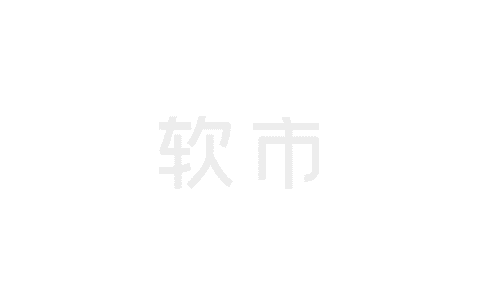
失效影响
失效影响与过程项的功能(系统、子系统、组件要素或过程名称)相关。失效影响被描述为顾客注意或体验的结果。PFMEA中应当明确指出可能影响安全或导致不符合法规的失效。
顾客可能是:
? 内部顾客(下一步操作/后续操作/操作目标)
? 外部顾客(下一层级/OEM/经销商)
? 立法机构
? 产品或产品最终用户/操作人员
以下失效影响会进行严重度评级:
1.您的工厂:假设在工厂内检测到失效,则该失效模式的影响(工厂会采取什么措施,例如: 废)
2.发运至工厂:假设在发运至下个工厂前未检测到失效,该失效模式的影响(下一个工厂会采取什么措施,例如:分拣)
3.最终用户:过程项影响的后果(最终用户关注、感觉、听到、闻到什么等,例如:车窗升得太慢)
在决定哪一组失效影响适用时, 应当提出以下问题会有帮助:
1.失效模式是否会对下游加工过程造成物理影响,或对设备或操作人员造成潜在伤害?
在后续任何顾客工厂内无法进行装配或与对手件对配。
若答案为是,则识别PFMEA中“您的工厂”和/或“发运至工厂”的制造影响。若答案为否,请回答第2个问题。
示例可包括:
? 无法在工位x处装配
? 无法在顾客端进行卡嵌
? 无法在顾客端进行对接
? 不能在工位x处钻孔
? 导致工位x处刀具过度磨损
? 工位x处设备损坏
2.对顾客端操作人员带来安全风险
注:若零件无法组装,则对最终用户不产生影响,第2个问题也不适用。
2.对最终用户有什么潜在影响?
独立于计划或实施的任何控制,包括错误或防错,请考虑导致最终用户注意或体验的过程项会发生什么。此类信息可能通过DFMEA获得。若某一影响来自DFMEA,则PFMEA中的产品影响描述应当与相应的DFMEA保持一致。
注:在某些情况下,分析团队可能并不了解最终用户影响(例如:目录零件、现货产品、第3级组件)。若不了解此类信息,应当根据产品功能和/或过程规范定义影响。
示例可包括:
? 噪声
? 很费劲
? 气味难闻
? 间歇运行
? 漏水
? 怠速不稳
? 无法调整
? 难以控制
? 外观不良
? 监管系统功能下降或失效
? 最终用户无法控制车辆
? 对最终用户的安全影响
3.若在到达最终用户前检测到失效影响,会发生什么?
当前或接收位置的失效影响也需要考虑在内。
识别PFMEA中“您的工厂”和/或“发运至工厂”的制造影响。
示例可包括:
? 停线
? 停止发运
? 整车候检
? 产品100% 废
? 生产线生产速度降低
? 增加人力以维持所需的生产线节拍
? 返工和返修
下一期会为您详细介绍失效模式、失效起因,敬请关注!
声明:本站部分文章及图片源自用户投稿,如本站任何资料有侵权请您尽早请联系jinwei@zod.com.cn进行处理,非常感谢!