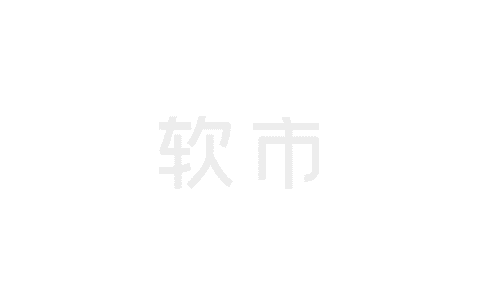
不久前,聪脉FMEA Master完成宁波福士汽车部件有限公司的新版FMEA介绍及D+PFMEA实战培训,此次培训是按照最新版的FMEA手册要求结合FMEA Master软件实操进行,培训受到了福士汽车员工的好评。
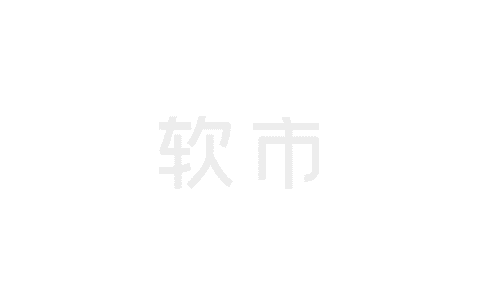
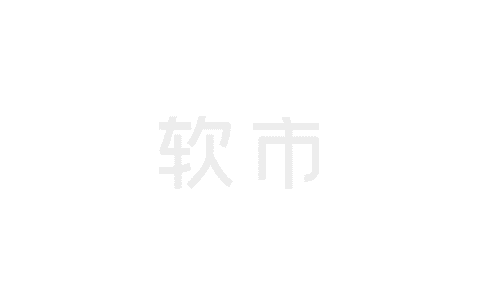
(宁波福士汽车现场培训照片)
那么,这次培训究竟为大家带来了哪些新的干货呢?小编现在就为大家揭晓。我们都知道,新版FMEA手册要求必须使用六步法来进行工作。其实,在我们实施FMEA的过程中,也有个“六步法”,了解了这些,做起FMEA来相信更加得心应手。
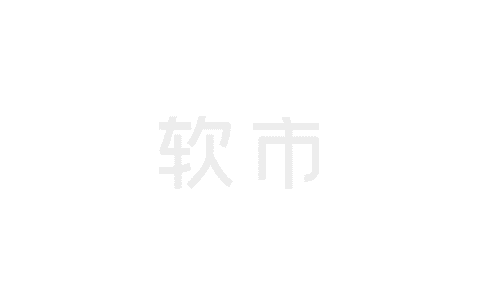
FMEA中的“1”
一种方法
FMEA分析方法,产品和过程设计风险评估和风险控制的一种方法。
一个中心
聚焦一个中心元素进行分析,可以是一个产品(DFMEA),也可以是一个过程(PFMEA)。
一份 告
FMEA分析过程的最终输出物是一份FMEA 告,用于展示和呈现FMEA分析内容。
一个团队
FMEA分析是团队性的活动,团队的成员由各个相关领域的人员组成。
FMEA中的“2”
两种假设
DFMEA:假设产品的制造和装配过程是合格的;假设产品的设计是满足设计意图的。
PFMEA:假设产品的设计是正确的;从上一工序流转来的产品是合格的。
两类措施
预防措施和探测措施(现行的和优化的)。
两种接口
内部接口:子系统与子系统之间、零件与零件之间、组织内各部门之间。
外部接口:系统与子系统之间、子系统与零件之间、组织与相关方之间。
两种特性
产品特性与过程特性。
FMEA中的“3”
三层结构
DFMEA:系统、子系统、零部件。
PFMEA:过程项目、工序/工步、要素。
三类失效
失效影响(FE)、失效模式(FM)、失效原因(FC)。
三个维度
严重度S、发生度O、探测度D。
三个等级
行动优先级AP:优先级高(H)、优先级中(M)、优先级低(L)。
FMEA中的“4”
四类因素
4M:人、机、料、环,造成失效的主要影响因素,但不仅限于。
四类要求
法规&安全要求、行业要求、相关方(顾客、供方等)要求、内部要求。
四个阶段
Plan :FMEA策划、组建团队、范围定义;
Do : 结构分析、功能分析、失效分析;
Check :风险分析;
Action :优化;
PDCA贯穿整个FMEA生命周期。
FMEA中的“5”
五种角色
管理者(如项目经理)、主管设计/工艺工程师、FMEA协调员、核心小组、扩展团队/专家。
五个“T”
团队(Team)、时间(Time)、意图(inTent)、工具(Tool)、任务(Task)。
五种时机
FMEA的导入时机:
1、新项目开发时;
2、应用或作业环境发生变化时;
3、发生工程变更时;
4、发现质量问题时;
5、定期评审、持续改进时。
FMEA中的“6”
六个步骤
1、范围定义:确定分析对象,包含什么、不包含什么;组建团队;创建任务;
2、结构分析:确定产品或过程的物理结构以及内外部接口或要素,识别内外部产品、过程及接口或要素关联关系;
3、功能分析:识别所有产品、过程及接口或要素的功能,并建立上下级功能关联,形成功能链或功能 ;
4、失效分析:分析并识别所有功能的失效模式,确定失效原因及失效影响,形成失效 络;
5、风险分析:制定失效预防措施和探测措施;评估失效风险,确定S/O/D等级;
6、优化:根据风险评估结果及AP行动要求,选择风险项目加入优化;制定优化措施并实施和验证;重新评估风险。
以上就是本次培训的部分知识分享,所以,FMEA“六步法”你get到了吗?
声明:本站部分文章及图片源自用户投稿,如本站任何资料有侵权请您尽早请联系jinwei@zod.com.cn进行处理,非常感谢!