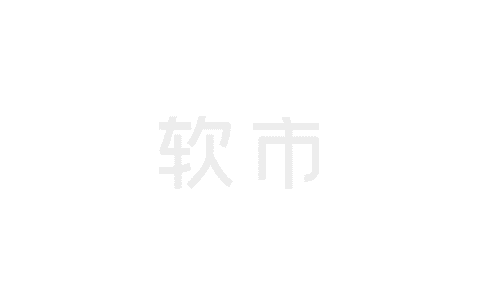
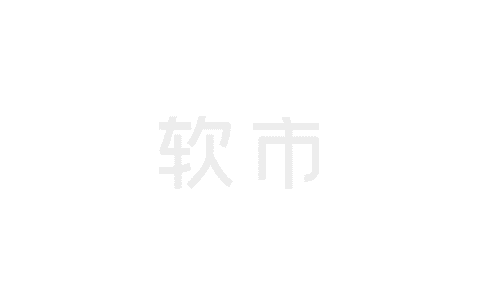
利用集成式仿真环境 # 高层摘要
通过使用飞机结构的端到端过程,在整个产品生命周期充分利用仿真功能,制造商已经能够及时、以可预测的性能提供创新产品。这让他们可以减少模型准备时间,缩短设计 – 分析迭代,评估不同学科之间的折衷方案,简化开发以便及时发货并改进设计质量。
? 高层摘要
绝大部分飞机企业工程部门都面临着根本性的挑战。这在飞机结构领域尤为明显,因为产品的复杂性日益提高,对于安全和认证的需求日益增加。机身结构分析的主要挑战在于自动化、标准化、追踪性和部署。
全局仿真过程意味着许多工程团队可以密切合作,从计算机辅助设计 (CAD) 定义到计算机辅助工程 (CAE) 模型和应力分析。使这一过程自动化,正是加快和改进设计仿真迭代效率的关键所在。
此外,导致飞机认证的飞机结构尺寸调整需要计算成千上万个结构分析。在应力分析过程中获取正确数据和使用正确工程方法、共享工作成果和发布应力 告缺乏一致性,致使认证困难重重且历时长久。过程标准化通过提高一致性并降低出错风险,帮助解决这一问题。
过程自动化和标准化是机身结构分析的重要难题,而维持特定数据、模型和过程 / 方法从概念到最终产品的可见性和追踪性一直是一大挑战。
最后,为保持竞争优势,全球化企业可以与供应商共享模型,而这也为数据安全带来真正的挑战。
如何实施飞机结构全局仿真过程
Siemens Digital Industries Software 提供有关飞机结构仿真的整套解决方案,帮助实现数据和结果的可追踪性,同时保持一致的全局过程控制。
Simcenter ? 产品组合是一系列综合仿真(加高级方法)测试和数据管理工具,可以简化全局仿真过程, 便于 CAD 几何体定义和提供 CAE 环境。
除了详细有限元模型 (FEM) 方法以外,最终用户可以使用分析工程方法库调整飞机结构组件尺寸。根据仿真数据和结果生成应力 告的功能,让最终用户可以从一致而集成的全局过程中获益,从而可以在整个设计周期节约时间。
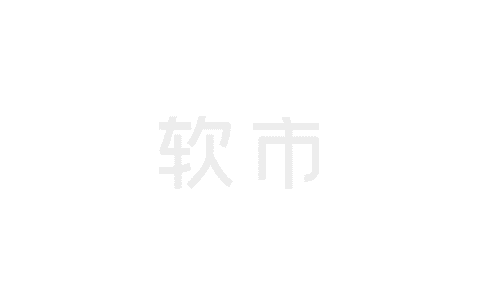
图 1:Siemens Digital Industries Software 工具用于简化全局仿真。
越来越多要在全球化团队中处理和共享的数据和结果、模型、仿真结果和工具通过 Teamcenter? 仿真软件管理和追踪。
Siemens Digital Industries Software 解决方案可以在全球范围内部署,因此,飞机原始设备制造商 (OEM) 可以通过为工程师们提供具备适当方法和工具的集成式环境来外包工作,并在供应链中形成竞争优势。
概括而言,机身结构分析中的自动化和标准化挑战可以通过 Siemens Digital Industries Software 产品解决, 因为它提供涵盖整个仿真链的集成式仿真环境,重点关注客户数据、知识和过程的捕获和追踪。
? 航空行业面临的挑战
航空航天企业面临着开发成本、改进项目交付性能和管理创新举措,同时便于管控产品质量的挑战。对于试图实现效率、质量、合规和成本突破的企业而言, 他们必须转变基于模型的工程过程。这是一个复杂而多维的问题,涉及不同过程、工具和组织之间的相互依赖。其目标是制定更为准确的决策、在项目周期中更早实现这些决策以及提高需求、功能、测试计划、验证和认证之类关键决策元素之间的关联和追踪。
第一项要求就是支持不同团队之间的端到端数字化连通和集成,让他们可以无缝执行业务工作,协同合作并在整个设计周期中管理数据访问。另一个重要方面就是创建产品架构、设计需求、测试计划和执行、仿真和验证、CAE 数据和过程管理之类不同学科和主题的数字化线程。
行业创新和领导企业正在构建和发起一些策略,用于关联业务目标与过程改进,此外还在制定能够产生短期价值和实现目标状态的特定举措。
开发成本在导致项目延迟方面存在的挑战,对于飞机结构领域尤为明显,因为产品的复杂性日益提高,对于安全和认证的需求日益增加。
? 成本压力增加
航空航天企业面临着开发成本、改进项目交付性能和管理创新举措并确保产品质量方面的挑战。
将新产品的开发和生产规划控制在预算和计划范围内, 对于任何一家飞机制造商而言都是一项挑战。飞机企业可能经历长达五年的项目延迟,这使制造商的工程时间显著延长,成本超支可能高达上亿美元。如图 3 所示,成本超支可能高达 48%。同时,制造商需要向客户支付的违约金可能高达数十亿美元(见图 3)。
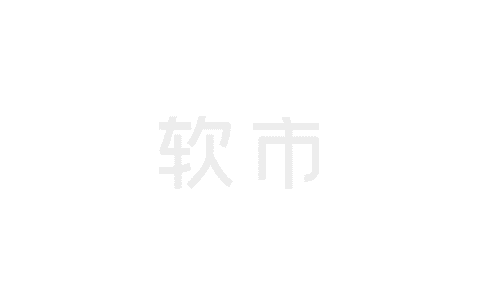
图 2:飞机开发成本和违约金示例。 ? 飞机结构开发项目
在可行性分析阶段,几种可能的飞机配置和匹配的机身架构和技术得以探索。例如,可以评估将引擎放在后部还是机翼盒上,或是评估对于结构使用复合材料还是金属。
一旦选定某种配置,我们就会转到概念阶段,将重点关注到结构拓扑和设计原则上(例如,结构框架的数量)。完整的飞机结构通过权衡研究逐步定义,从而评价几种准则之间的最佳权衡。
总体机架一旦确定,就可以开始结构细节定义的最终设计。例如,考虑减层的堆叠顺序或详细桁条剖面(如腹板高度、腹板和支柱厚度)。
确定飞机的详细尺寸之后,权威机构将根据关键文档评估飞机的审批和认证。这属于开发阶段。
在每个环节,都时常需要对设计和载荷更新进行迭代和返工,以便实现最佳设计和认证需求,而这也导致额外延迟并影响整个开发过程。
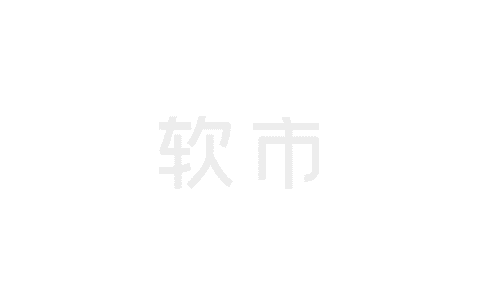
图 3:飞机结构开发项目的典型阶段。 ? 对于结构分析过程的影响
由于飞机制造商的数量不断增加以及新厂商的不断涌现,以更短的交付周期和具有竞争力的成本交付,这方面的压力倍增。
此外,材料和设计复杂性的不断提高,导致结构分析需求增加。工程比已经从 5 个设计师:1 个应力工程师增加到 1 个工程师:2 个应力工程师。
除此以外,认证环境和安全标准也越来越严格。
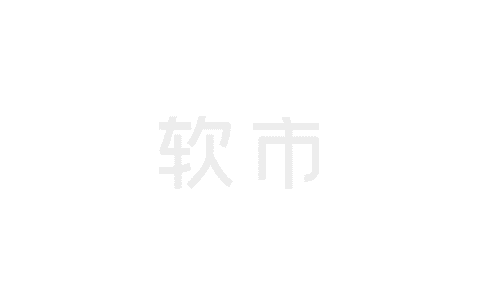
图 4:商用飞机按大小划分的竞争格局(Cay-Bernhard Frank 与 A.T.Kearney 联合研究)。
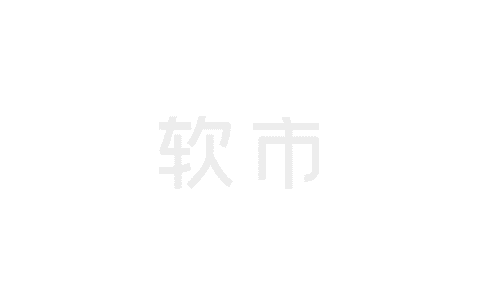
图 5:波音工程师主管兼项目经理基恩 · 巴森海耶认为复杂性推动了分析需求。 ? 飞机结构分析中的难题
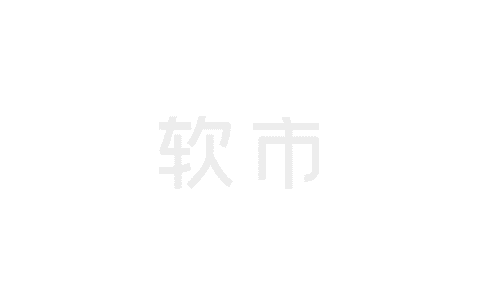
图 6:商用飞机非重复性成本分配(雅各布 · 马基什)
商用飞机(30% 是军用飞机)有 60% 的非重复性成本花费在结构上,这就意味着,任何结构分析过程方面的改进都会对减少延迟和成本超支产生重要影响。
为了突出结构分析过程方面潜在的改进,让我们一起来看看典型飞机结构过程。
? 典型飞机结构过程与挑战
下图显示了从 CAD 基础架构、内部载荷有限元模型
(或全局有限元模型)生成到应力和结构评估分析这一简化过程。
典型的飞机结构过程主要涉及四个不同学科:设计 /CAD、载荷、有限元模型连同有限元模型生成和有限元分析、安全裕度 (MoS) 计算。
设计 – 根据公司流程对 CAD 模型进行手动更新或者参数化。但是,CAD 数据并不是主要用于仿真。
准备仿真几何体非常耗时,因为它可能花费 20% 的分析时间。能够迅速了解任何设计更改对于完整过程的影响,这也至关重要。
从仿真角度对 CAD 几何体进行参数化,而不是依赖于设计师意图,对于在整个过程中减少几何体准备时间价值重大。
外部载荷计算(飞行理论,包括气动弹性学)– 外部载荷有限元模型用于主要结构刚度和质量效应的线性静态、动态和颤振分析。这帮助实现了载荷与更为详细的内部载荷有限元模型的映射。
声明:本站部分文章及图片源自用户投稿,如本站任何资料有侵权请您尽早请联系jinwei@zod.com.cn进行处理,非常感谢!