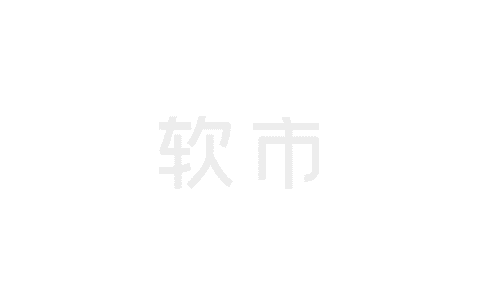
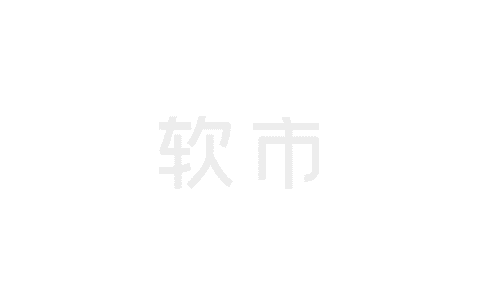
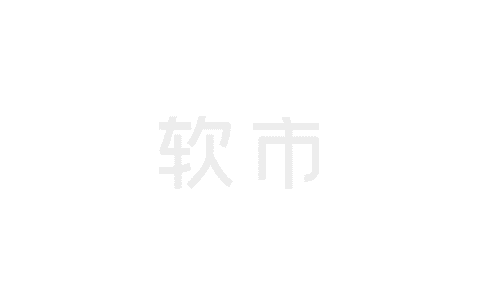
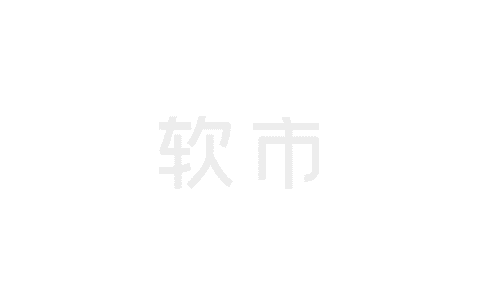
图 2:冷板设计的五种可能几何配置。 这就要求冷板、管道系统和热交换器必须同时设计,以确定其彼此如何相互作用。冷板的设计验证通过三维CFD 进行,以找到内部几何形状的最佳选择 —— 它是否应包含立柱、翅片或开放通道,以及翅片是对齐还是交错。虽然三维 CFD 能提供冷板性能的非常精确的结果, 但在三维 CFD 中对整个冷却系统进行建模是不切实际的。 格数量将十分巨大,仿真时间将会长得不合理。 对于系统的其余部分,组件位置、尺寸和热交换器性能是关键方面,一维方法更合适。 要回答的问题是:若同时使用一维和三维 CFD 工具进行仿真,是否有合理且高效的方法来优化整个系统?
图 4:采用液冷冷板的驾驶舱特写图。 蓝线代表含有要被送到冷板的冷 PAO 的管道,红线代表热 PAO 离开冷板并进入机翼传感器和空气循环机,绿线代表用于冷却 PAO 的燃油回路。 为了优化系统,将考虑五种不同的冷板设计。这些设计如图 5 所示。 图 5:冷板设计选择。 在三维 CFD 中评估这些设计后,将比较其独立性能,以及它们作为一个整体在系统中的表现。 A. 评估冷板设计 冷板热设计的主要影响因素包括流体速度、传热面积和SWaP-C,即尺寸、重量、功耗和成本。 流体速度的增加会提高传热系数,进而提高热流量,从而降低芯片温度。但与此同时,较高的流速也会导致压降增加,从而增加泵的能耗。 通过增加立柱或翅片之类的增强表面,可以显著改变传热表面积,如图 5 所示。这些增强表面的有效性也会受到其排列的影响,例如是否对齐或交错。这会增加热流量,但同时压降也会增加。例如,与对齐排列相比,交错排列的热流量通常更高,但同时压降也更大。 增强特性对 SWaP-C 也会产生重大影响。构造增强表面需要额外的材料,因此额外的表面积可能影响冷板的尺寸和重量;另外工具和制造要求也更复杂,导致成本上升。 B. 冷板仿真 冷板和相关电子元件(IGBT 和二极管)采用 Siemens NX 3D CAD 程序构建,并利用 Simcenter FLOEFD 3D CFD 软件进行 格划分。Simcenter FLOEFD 是 CAD 嵌入式 CFD 工具,所有 格划分和仿真都是从 NX 用户界面完成。 IGBT 芯片和二极管是热源,在本例中分别为 360 W 和144 W。对于初始分析,入口流速设定为 5 升/秒。 图 6:液冷航空电子设备 格示例以及 NX 和 Simcenter FLOEFD 中的结果。 从表 1 中可以看出,采用 4 核计算机时,此模型完成一次分析运行的时间为 4.5 小时,用户交互时间为 2.5 小时。我们使用了 16 核计算机,执行了 16 次运行参数研究,完成时间为 16 小时。 表 1:Simcenter FLOEFD 液冷冷板三维 CFD 仿真的分析统计。 C. 冷板仿真 对每种冷板设计进行仿真,体积流量为 5 升/分钟,并且 比较结果。图 7 显示了每种设计的压降与元件温度的关系,气泡大小代表每种设计的相对重量。很容易看出,没有任何增强传热表面的设计,其重量和压降均为最低,但工作温度也最高,显著高于所有其他设计。其他设计的工作温度非常相近,但压降差异很大,交错翅片设计的压降最高,重量最重。 图 7:压降与工作温度和冷板设计重量的关系。气泡大小代表冷板的相对重量 另外,通过将体积流量边界条件从 0.1 升/分钟变为 5 升/ 分钟,对每种设计进行了参数研究。每种设计的体积流量、温度与压降的结果如图 8 所示。该图表明,所有具 有增强传热表面的冷板设计在 1.5 升/分钟及以上的流量下散热性能相似,但对齐和交错设计之间的压降有显著差异,交错设计的压降比对齐设计高出 50% 到 100%。 图 8:体积流量与工作温度和冷板设计压降的关系。(实线 – 温度。虚线 – 压降) 最后绘制了冷却剂入口温度与元件温度的关系图。它表明,随着入口温度增加,元件温度呈线性增加,所有设计都有相似的变化率。 图 9:冷却剂入口温度与元件温度的关系。 比较参数研究的结果,很明显有两种设计比其他设计表现更好。这两种设计具有对齐配置的增强传热表面(立柱或翅片)。这些是进行特征提取和导入到一维仿真模型中的候选设计。 图 10:冷板设计最佳选择。立柱对齐(左)。翅片对齐(右)。 D.构建试验设计 为了在一维仿真模型中研究冷板设计的性能,必须将性能特征编译成可通过一维仿真读取和评估的响应面。所需的响应面数量将取决于变量的数量、可能流动路径的数量以及变量彼此之间的依赖关系。对于冷板,仅需要一个响应面。 图 11:对齐立柱冷板的响应面映射。 为了创建响应面,为每个冷板构建一个试验设计。Simcenter FLOEFD 的集成界面可实现此目的。用户只需选择要改变的输入、其值的变化范围以及每个变量的增量变化。然后,软件就会构建输入变量矩阵并确定需要运行的仿真数量。对于冷板,每个选项总共需要 20 次运行。 图 12:Simcenter FLOEFD 中的试验设计界面。 E. 创建响应面 完成试验设计后,便可生成响应面。具体做法可以是将结果导出到电子表格中,然后在一维仿真工具中生成这些曲线。本研究使用的一维工具是 Siemens 的 Simcenter Flomaster;Simcenter FLOEFD 具有导出功能,可以生成并导出响应面数据,Simcenter Flomaster 可以直接读取数据。这样可简化流程,并有助于消除数据输入错误。 此功能可从 DOE 界面访问,生成过程大约需要一分钟。 F. 将响应面纳入一维仿真模型 使用的一维仿真工具不同,将响应面数据引入模型的方法可能不同。几乎所有工具都有某种表格数据输入和表面拟合功能,支持手动输入或从电子表格导入。 图 13:用于生成响应曲面的数据输入界面示例。 有些人使用的另一个工作流程是通过功能实物模型接口(FMI) 和功能实物模型单元 (FMU) 创建。这些是预编译模型,基于与工具无关的标准,支持模型交换和动态模型(组合使用 xml 文件和编译过的 C 代码)的协同仿真。 图 14:FMU 导入和创建。 这是 Simcenter FLOEFD 和 Simcenter Flomaster 导入功能背后的方法。为将基于响应面的元件放入数据库,可使用一个导入接口从 Simcenter FLOEFD 中定位导出的文件。然后,该接口将构建访问响应面数据所需的分析模型,并将其保存到元件数据库中。完成此工作后,新元件便可像使用该工具中的任何标准元件模型一样使用。 G. 瞬态飞行轨迹仿真 为了确定这两种冷板设计中哪一种对系统最佳,使用上述方法将两者引入一维工具中并代入散热系统模型。 每个冷板使用相同的飞行轨迹加以运行,并检查其对系统的影响。这是一个很短的飞行轨迹,但有几个快速的高程变化,以便展现高度对燃油系统的影响,判断能否提供所需的散热能力。 图 15:仿真飞行轨迹。 H. 系统级冷板设计比较 我们考察了两个参数来确定哪个冷板是最佳选择。第一个参数是冷却剂离开冷板时的出口温度。两种情形中冷板入口处的温度是相同的(所有其他参数保持恒定),因此较高的出口温度意味着几何形状差异导致对冷却剂的排热量较多。 图 16:一维仿真中的冷板出口温度。 图 16 显示,对齐翅片设计的出口温度比对齐立柱设计高出 8 华氏度。 考察的第二个参数是冷板出口处的压力。对齐立柱设计的压力较高,因此压降较低,但差异不显著。 图 17:一维仿真中的冷板出口压力。 从这些参数可以看出,对齐翅片设计对于该系统是最佳的。 声明:本站部分文章及图片源自用户投稿,如本站任何资料有侵权请您尽早请联系jinwei@zod.com.cn进行处理,非常感谢!